At Metalsin, we have been supplying a series of water valves to Indonesia’s waterworks industry. Most of these water valves are made from ductile iron, which faces accelerated corrosion due to a combination of environmental factors inherent to the region’s tropical, archipelagic climate:
- Persistent Moisture and High Humidity: The consistently high humidity and frequent, heavy rainfall create a persistently moist environment. This constant exposure to moisture promotes the formation of corrosive electrolytic films on the valve surfaces, thereby accelerating the oxidation process of the ductile iron.
- Salt Exposure in Coastal Areas: In many Indonesian coastal regions, salt-laden winds deposit chloride ions on the valves. Chloride ions are particularly aggressive because they can penetrate and disrupt the naturally forming passive oxide layer on ductile iron. Once this barrier is compromised, localized pitting corrosion occurs, which can rapidly degrade the material’s structural integrity.
- Cyclic Wet-Dry Conditions: The tropical climate often results in repetitive cycles of wetting and drying. Each cycle stresses the protective coatings applied to the valves—through thermal expansion and contraction—and can cause micro-cracks. These breaches allow moisture and chlorides to infiltrate the metal surface, further promoting corrosion.
- Aggressive Water Chemistry: The water in some areas may contain elevated levels of dissolved solids, including chlorides and sulfates, which contribute to a corrosive water chemistry. When such water flows through valves, it not only causes general corrosion but can also lead to localized corrosion phenomena such as pitting and crevice corrosion.
- Galvanic Corrosion Risks: In many waterworks installations, ductile iron valves are connected to components made from other metals. In the presence of an electrolyte (e.g., saltwater), this dissimilar metal pairing can initiate galvanic corrosion, where the less noble metal corrodes preferentially.
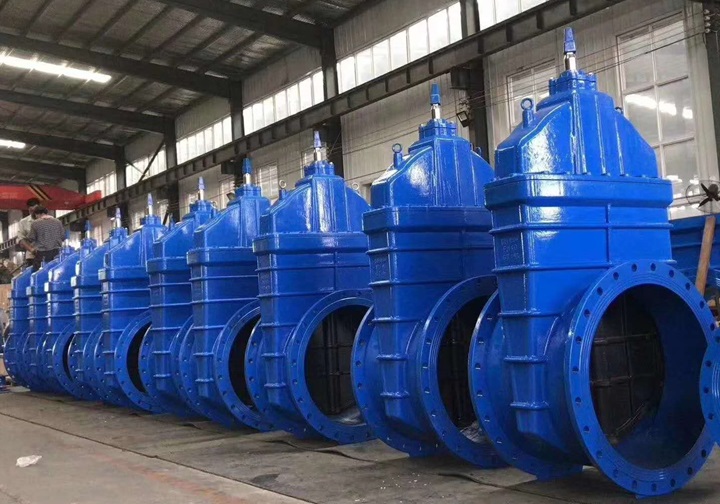
Liquid epoxy coating ductile iron resilient-seated gate valves, non rising stem, BS 5163 DN500 PN16, supplied to Surabaya, Indonesia.
To cope with these corrosion challenges, Metalsin adopts several high-performance coating technologies to protect the ductile iron water valves:
- Multi-Layer Coating Systems: A proven strategy is to apply a multi-layer coating on the external surface of the ductile iron valves that forms a durable barrier between the metal and the corrosive environment. Such a typical system might include: (1) Zinc-Rich Primer: This sacrificial layer provides galvanic protection by preferentially corroding, thereby shielding the underlying ductile iron. (2) Epoxy Resin Intermediate: Two-component, high-build epoxy coatings offer excellent adhesion, chemical resistance, and a continuous barrier against salt and moisture. Such epoxy systems are often engineered to meet severe corrosive conditions and have been used successfully in fire protection valves and industrial applications. (3) Topcoat (Polyurethane or Fluoropolymer): A weather-resistant topcoat improves UV resistance and further seals the underlying layers, extending the service life of the valve.
- Fusion Bonded Epoxy (FBE) Coatings: Originally developed for pipelines, FBE coatings are thermoset powder coatings that melt and chemically cure to form an impermeable, cross-linked barrier on both exterior and interior surfaces of ductile iron valves. They combine excellent adhesion with a high resistance to both chemical attack and mechanical wear, making them suitable for harsh, salt spray environments.
- Liquid Epoxy Resin Coatings: Liquid epoxy coatings—typically applied as two-part systems—are valued for their robust protective film, high hardness, and excellent chemical resistance. Their formulation can be optimized (e.g., high solids, room-temperature cure) to ensure proper film formation even in humid coastal conditions. These coatings, when applied over well-prepared surfaces, minimize direct contact between the corrosive medium and the ductile iron valve surface. Both the FBE and liquid epoxy coating shall be furnished in accordance with AWWA C550 and NSF/ANSI 61.