What’re Ductile Iron Grooved Fittings?
Ductile iron grooved fittings are mechanical connectors made from ductile iron, designed to join pipes in a piping system using a grooved coupling method. These fittings leverage the strength of ductile iron and the efficiency of grooved mechanical joints for secure, adaptable connections.
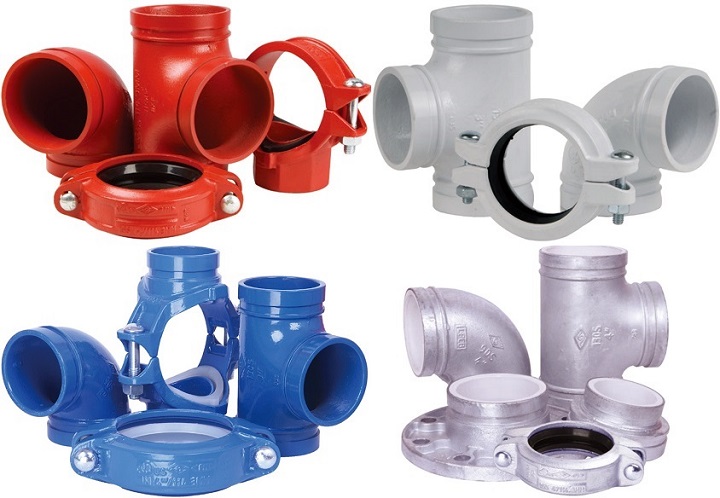
Ductile iron grooved fittings with various coatings: electrophoretic coated, epoxy coated, or hot-dipped galvanization coated.
Ductile iron is a refined form of cast iron produced by adding magnesium or cerium to the molten metal, which transforms the graphite structure into nodular or spheroidal shapes. This change not only improves ductility but also increases toughness and resistance to impact and fatigue compared to traditional cast iron. Grooved fittings exploit these material advantages by incorporating precision-machined grooves on pipe ends that mate with corresponding grooves on couplings or fittings. When coupled with a gasket and fasteners, the joint creates a secure, leak-resistant connection without the need for welding or flanging.
Product Forms & Technical Specifications
*Ductile iron grooved fittings can be furnished in the product forms of coupling, elbow, tee, cross, reducer, cap, flange and flange adaptor, etc. The groove dimension are machined in accordance with ISO 6182 and AWWA C606; The threads are tapped in accordance with ASME B1.20.1, ISO 7-1, and GB/T 7306.
Material & Manufacture
The production of ductile iron grooved fittings involves a series of precise steps to ensure strength, durability, and compatibility with grooved coupling systems. Below is a detailed breakdown of the manufacturing process:
- Raw material preparation begins with melting iron in a furnace (such as a cupola, electric arc, or induction furnace). Following the melting process, nodularization is achieved by adding magnesium or cerium to the molten iron, which transforms graphite into nodular (spheroidal) structures and enhances both ductility and toughness. Additionally, inoculation is performed by introducing silicon-based alloys (for example, ferrosilicon) to refine the graphite formation and further improve the mechanical properties of the iron.
- In the casting process, sand casting is commonly used with resin-bonded sand molds for precision; these molds are designed using CAD software to accurately match the geometry of fittings such as elbows, tees, and reducers. Molten ductile iron is poured into the molds, and controlled cooling is implemented to prevent internal stresses and ensure uniformity.
- After casting, the fettling process begins with the shakeout, where the castings are removed from the molds; then, excess material such as gates, risers, and flash is removed using abrasive tools during grinding, and finally, burrs and rough edges are eliminated to smooth the surface and prepare the castings for machining.
- In the machining stage, CNC machining is employed to precisely shape critical surfaces—including grooves, threads, and flanges—to strict tolerances. Specialized tools are used to cut circumferential grooves into the fitting ends that match coupling dimensions as defined by AWWA C606 standards, and threads or other connection points are added if required.
- In the heat treatment stage, fittings are annealed by heating them to 900–950°C and slowly cooling them to relieve residual stresses from casting and machining; optionally, normalizing is performed to enhance hardness and achieve a uniform microstructure. Subsequently, surface treatment is carried out by first shot blasting the surface to clean and roughen it for improved coating adhesion, followed by applying anti-corrosion coatings—either an epoxy or powder coating applied electrostatically and baked for enhanced durability, or galvanizing with a zinc coating for extreme environments such as wastewater systems.
- The grooved fittings undergo quality control through non-destructive testing (using ultrasonic or X-ray methods) to detect internal defects, dimensional checks with CMM or gauges to verify groove dimensions, thread pitch, and overall size, and pressure tests to ensure leak-proof performance. Optionally, pre-assembled components such as gaskets and bolts are attached for turnkey solutions. Finally, the ductile iron grooved fittings are packed in cartons, and labeled according to industry standards for shipping.
Advantages & Applications
Ductile iron grooved fittings offer exceptional leak resistance through tight groove tolerances, ensuring secure coupling seals. Their durability is enhanced by heat treatment and protective coatings, making them ideal for harsh conditions. With standardized dimensions, these fittings provide excellent interchangeability across various piping systems. Widely used in fire protection, HVAC, water distribution, oil and gas pipelines, and industrial plants, they combine advanced metallurgy, precision machining, and rigorous testing to deliver reliable performance while simplifying installation and maintenance.