An AWWA C213 FBE coating steel water pipe refers to a steel pipe that has been coated with fusion-bonded epoxy (FBE) according to the specifications outlined in the AWWA C213 standard. It is commonly used in water transmission and distribution systems. The FBE coating provides excellent resistance against corrosion, abrasion, and chemical attack, ensuring the durability and longevity of the steel pipe in various water-related applications. Moreover, FBE coatings are formulated to be non-toxic and safe for contact with potable water. They do not leach harmful chemicals or contaminants into the water, ensuring that the water remains safe for consumption.
Materials
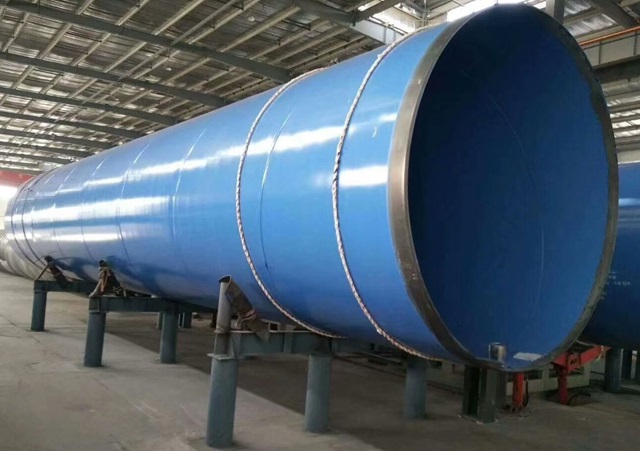
FBE coating SSAW steel water pipes; both interior & exterior are FBE coated according to AWWA C213; 36″ STD L=6m; supplied to Jakarta, Indonesia.
The materials required for the production of AWWA C213 FBE coating steel water pipes include the base pipe and the epoxy powder:
- Base Pipe: The base pipe furnished shall be made in accordance with AWWA C200. It can be a seamless pipe, ERW pipe, LSAW pipe, or SSAW pipe, made from a series of carbon steel grades such as ASTM A106; ASTM A53; ASTM A333 Grade 6; ASTM A516 Grade 55, 60, 65, 70; API 5L Gr.B, X42, X46, X52, X56, X60, X65, X70. The pipes are furnished in 6m or 12m. Custom lengths are also available upon request.
- Epoxy Powder: The epoxy powder shall consist of a one-component fusion-bonded material comprising epoxy resin, curing agents, catalysts, fillers, colorants, flow-control agents, and ultraviolet-light-resistant agents, that when applied to the preheated substrate, will uniformly coalesce and cure to produce a homogeneous film. Generally, the requirements for physical properties of the epoxy powder include: (1) Specific gravity at 73°F [23°C]: 1.2~1.8; (2) Sieve analysis (percent retained on 100-mesh screen): ≤2.0; (3) Gel time at 400°F±5°F [204°C±2°C]: 7 seconds.
Production Process
The production process of fusion bonded epoxy (FBE) coatings for steel water pipes involves several key steps to ensure the coating effectively protects the pipes from corrosion:
- Surface Preparation: The steel pipe surface must be thoroughly cleaned to remove rust, scale, oil, grease, mud, mill lacquer, wax, coal tar, asphalt, chlorides, and any other foreign material or combustible contaminants that could ignite at the fusion-bonded epoxy application temperatures. This is typically done through blast cleaning, which creates a rough surface profile to enhance the adhesion of the coating.
- Heating: Once cleaned, the steel water pipe is heated to a specific temperature, usually between 350-500°F (about 177-260°C). This temperature is crucial for the subsequent powder application and fusion bonding.
- FBE Powder Application: The FBE coating is applied as an electrically charged dry powder. The charge helps the powder adhere to the heated pipe surface.
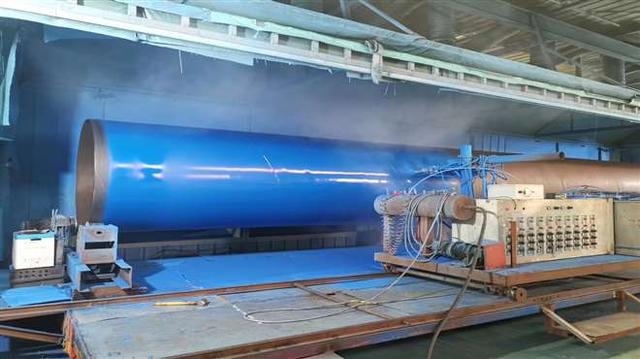
The production scene of FBE coating: the application of epoxy powder to the preheated exterior surface of the steel pipe.
- Melting & Fusion Bonding: As the powder comes into contact with the hot pipe, it melts and transforms into a liquid form. This liquid FBE film then wets and flows onto the steel surface, ensuring complete coverage.
- Chemical Cross-Linking: The heat assists in initiating a chemical cross-linking reaction within the FBE coating, which is irreversible. This reaction ensures that once the coating has cured, it cannot return to its original powder form, even if further heating is applied.
- Curing: The final step is the curing of the FBE coating, where it solidifies to form a durable, protective layer that is resistant to corrosion, abrasion, and chemical attack. This layer, if applied to the interior of the pipe, also helps to improve the flow of fluid through the pipe by reducing friction and turbulence. The epoxy powder shall be applied to the steel water pipe at a uniform cured-film thickness of not less than 12 mil (305 μm) on the exterior or interior of the pipe surface.
Subsequent inspection and tests shall be conducted to ensure a strong, uniform coating that adheres firmly to the steel pipe, providing long-term protection against environmental factors that can cause corrosion and degradation.